A Spoke in the Spanners
Let's get this straight - a disc wheel is NOT the latest technology. It is the first - a slice off the end of a log started it all, and lives on in the indoor velodrome. Indoor, because riding one those in the great outdoors is asking for trouble. Anything other than a direct head or tailwind, and you feel it in the wheel.
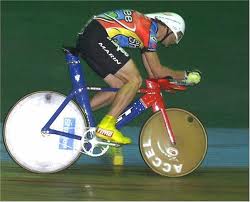
But, solid wheels are heavy, so the obvious thing to do is to remove mass from the disc. Lots of holes, and you have the development of spokes. Of course, a spoke is a separate piece of the wheel, and with spokes you get a wheel that is made of many pieces - the hub, a rim, and a whole pile of spokes. Chariot wheels, cartwheels, car wheels, bike wheels. yet, there are some differences, and it comes down to radial or cross.
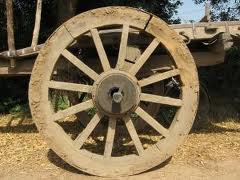
Tension, Wheel Design and Truing
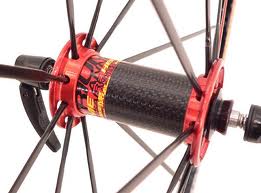
Easing spoke tension is not, then, a good strategy for reducing flexion. But you cannot over-tension spokes, either. Wind up anything beyond snapping point, and it will snap. Or other damage. And this brings us to spoke number.
Spoke Number
Front wheels are typically under less stress than the rear wheels, which are pretty much directly under your butt. My favourite front wheel has sixteen blade spokes laced radially. The matched rear wheel popped a spoke once a month. I tried an eighteen-spoke build on the rear, but for my weight it was inadequate. The spokes did not break, but the tension that I had to run them at led to the spoke nipples being pulled through the rim eyelets. Fail. The next build was a 24 spoke Gipiemme, with the customary triplet-spoke lacing. Almost there, but hairline cracks appeared around the eyelets, so it is now an emergency spare wheel.My current build is a 28-spoke with 2-cross lacing, and after the first 4000 km does not need any truing adjustments, so I am sticking with this pattern.
Lacing: Radial or Cross
Radial patterns have maximum strength when the spokes are shorter and more numerous. A shorter spoke length, with a 700c road rim, can only be achieved three ways - extend the hub, deepen the rim, or both. High-end carbon rims with side-anchor spokes and milled hubs take care of this, but they will also take care of any plans to pay off your mortgage, too. A cross-over pattern gives the wheel added strength, as the lacing involves passing the spokes alternately behind and in front of each other so that, when under tension, the spokes press against and support each other when flexing under tension - try arching your back while standing against a wall. You'll soon get the idea.![]() |
Lacing guide from Sheldon Brown |
Simply, the more cross-overs the stronger the wheel. part of this comes from the tangential positioning of the spokes. Rather than aligned along the radius of the wheel, the spoke is anchored further around the hub, almost at a tangent to the hub edge. As a result, the spoke that is under direct compressive tension is transmitting the compressive force outwards to the hub edge, triangulating the force away from the hub. Rather than a linear compression, the downwards force is shifted sideways, with the spokes held against excessive flexion by the crossing spokes, thereby minimising flexing and fatigue.
For detailed discussion on wheelbuilding and spoke cross patterns, two good sites include the famed, late Sheldon Brown, and the Spoke and Wheel site.
Many wheels are built with three-cross, but I find a two-cross pattern fine for my build and weight. So, how long?
Spoke Length
The easy way is to use an online spoke-length calculator. Two that I use are Edd.com, and the DT-Swiss calculator. If your hub and rims are already in the calculator databases, you merely enter the specific details - number of spokes and how many cross-overs. If your hub or rim is not in the database, you can manually enter the hub dimensions. I used both, and compared for consistency before ordering (they matched).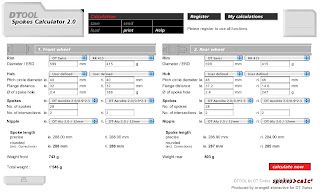
Yeah, you say, easy for me to say. I teach high-school math for a living. I'm a trained professional (trust me, I know what I'm doing...). So, use the calculator. Unless you have an unusual lacing pattern, such as the Gipiemme triple on the Campagnolo wheel. Then you have to do it the long way, as I did.
Purchase
Round spokes are the order of the day. There have been studies made about the aerodynamic qualities of different spokes and yes, round spokes generate a certain amount of turbulence behind the moving spoke. Flat spokes are just that - round spokes that have been through rollers to squash them flat. These have a reduced profile with reduced turbulence. The top end spokes are the aero variety which, rather than just flattened, have been shaped to give an oval profile. The sloping surfaces reduce the low-pressure turbulence zone behind the moving spoke, and offer some limited aerodynamic benefits. But, as always, there are conditions. Namely, if you use aero or flats, you must have radial lacing. As indicated earlier, a radial pattern is either too weak or too expensive to reconcile with my budget and common sense. I am not an elite rider, and there is little point in pretending that I am anything more than a mid-pack rider.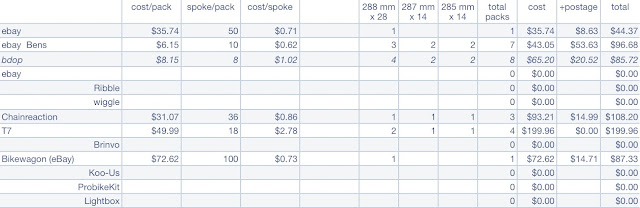
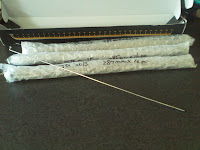
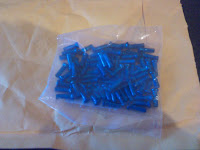
I now have the hubs, rims, spokes and nipples needed to build a matched pair of wheels, and the wheel stand to do it with. All is good.
Next mission is to get back to the drive train, and find a pair of shifters.
No comments:
Post a Comment